Kaizen, a Japanese philosophy of continuous improvement, has become increasingly popular in the world of production companies. Companies around the world have adopted Kaizen philosophy as a means to improve their production processes. At its core, Kaizen is focused on making continuous improvements in all aspects of a production company’s operations. This philosophy aims to improve quality and customer value in a company’s products or services, as well as reduce inefficiencies, waste and costs.
The term “Kaizen” comes from the Japanese words kai and zen, which together mean “change for the better”. This philosophy requires a cultural shift and the involvement of all employees. In Kaizen, employees are engaged in the process of identifying areas for improvement and developing solutions to address them.
Kaizen is not a one-time event but rather an ongoing process of improvement.
Suárez-Barraza and Lingham summarise the Kaizen methodology as involving all employees in the organization, making small incremental improvements to methods and processes of work, and emphasizing the importance of team-driven problem-solving.
The Kaizen process is the journey towards continuous improvement and involves everyone in the organization, from managers to lower-level employees. One of the reasons Kaizen is so effective is that it assumes those closest to the work process are best suited to identify areas for improvement and implement action plans. Kaizen methodology also emphasizes the importance of making small changes over time rather than large-scale changes all at once.Kaizen has a significant impact on production companies’ operations. It helps to create a culture of continuous improvement and innovation within the organization. Furthermore, participating in Kaizen activities provides employees with new knowledge, skills, and abilities that can be applied to subsequent problem-solving tasks. Successful implementation of Kaizen activities in an organization relies on direct communication between all stakeholders.
However, not everyone agrees that Kaizen is the most effective approach for production companies. Some argue that the focus on small incremental improvements may not lead to significant cost savings or increased efficiency in the long run. They claim that larger-scale changes might be necessary to keep up with competitors and remain profitable. Nonetheless, companies that have implemented Kaizen methodology have shown remarkable improvements in their manufacturing processes.
Additionally, some critics point out that implementing Kaizen can be time-consuming and expensive for organizations already struggling to meet their goals. It requires extensive training for all employees involved, which takes away from valuable work hours. Despite these criticisms, Kaizen has proven to be a successful approach for many production companies.
Moreover, some studies have shown mixed results when it comes to the success of implementing Kaizen in production companies.
Try WinWinBalance for free for 30 days and improve Kaizen pfhilosophy in your organisation like WinWin Clients!
However, overall, the benefits of Kaizen far outweigh its drawbacks. In addition to improving productivity and lowering costs in the long run, it also promotes a sense of ownership among employees who are involved in decision-making processes and problem-solving tasks. The redistribution of power between managers and workers results in improved communication and collaboration within an organization.
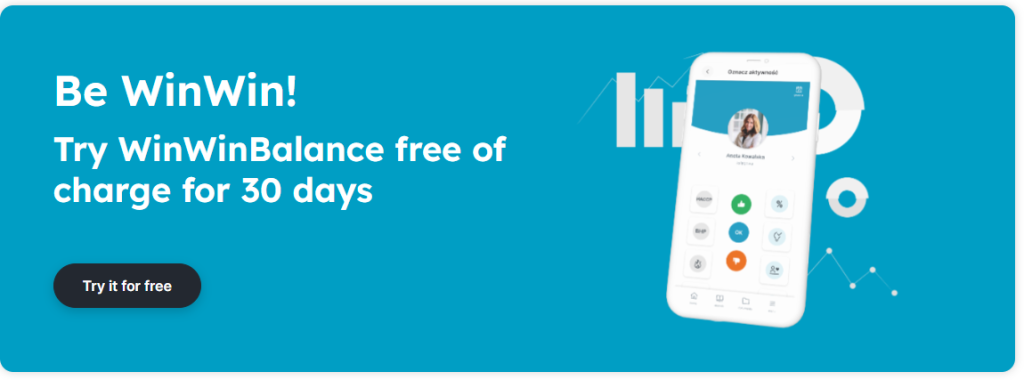
Moreover, Kaizen practices use low-cost solutions that don’t require significant investments like expensive equipment or sophisticated techniques. It is essential for companies to involve all employees at different levels in identifying inefficiencies through continuous improvement activities.
Kaizen is not a one-time event but rather an ongoing process of improvement.
Suárez-Barraza and Lingham summarise the Kaizen methodology as involving all employees in the organization, making small incremental improvements to methods and processes of work, and emphasizing the importance of team-driven problem-solving.
The Kaizen process is the journey towards continuous improvement and involves everyone in the organization, from managers to lower-level employees. One of the reasons Kaizen is so effective is that it assumes those closest to the work process are best suited to identify areas for improvement and implement action plans. Kaizen methodology also emphasizes the importance of making small changes over time rather than large-scale changes all at once.Kaizen has a significant impact on production companies’ operations. It helps to create a culture of continuous improvement and innovation within the organization. Furthermore, participating in Kaizen activities provides employees with new knowledge, skills, and abilities that can be applied to subsequent problem-solving tasks. Successful implementation of Kaizen activities in an organization relies on direct communication between all stakeholders.
Many companies worldwide have adopted Kaizen methodology to improve their production processes. One such company that has seen remarkable success through the implementation of Kaizen is Toyota. Toyota’s continuous improvement culture, including kaizen activities, has helped them become one of the most efficient and profitable car manufacturers in the world.
Other companies that have successfully integrated kaizen principles into their production systems include Honda, Intel Corporation, and Boeing Co. These firms operate in highly competitive industries where operational efficiency is essential for remaining competitive.
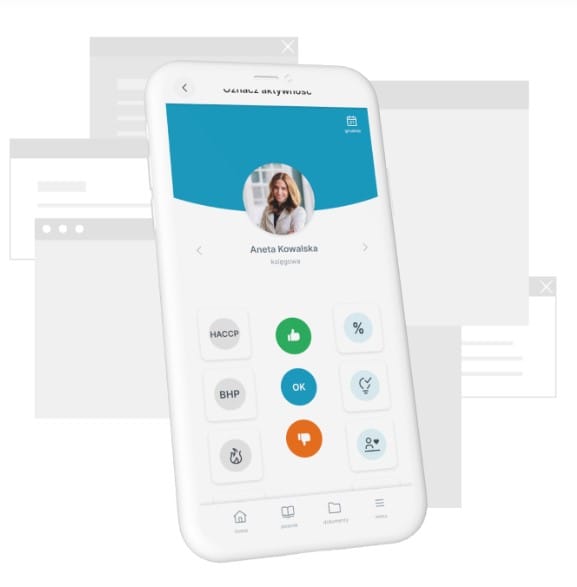
However, not everyone agrees that Kaizen is the most effective approach for production companies. Some argue that the focus on small incremental improvements may not lead to significant cost savings or increased efficiency in the long run. They claim that larger-scale changes might be necessary to keep up with competitors and remain profitable. Nonetheless, companies that have implemented Kaizen methodology have shown remarkable improvements in their manufacturing processes.
Additionally, some critics point out that implementing Kaizen can be time-consuming and expensive for organizations already struggling to meet their goals. It requires extensive training for all employees involved, which takes away from valuable work hours. Despite these criticisms, Kaizen has proven to be a successful approach for many production companies.
Moreover, some studies have shown mixed results when it comes to the success of implementing Kaizen in production companies.
Kaizen is a valuable approach for production companies seeking to improve their manufacturing processes. It provides numerous benefits including cost reduction, better product quality, higher productivity levels and more motivated employees. While some critics question its effectiveness for long-term gains or argue it may be costly or time-consuming at the outset,, the majority of research supports these benefits over time through continuous improvement activities. Nevertheless, successful implementation requires strong communication channels.
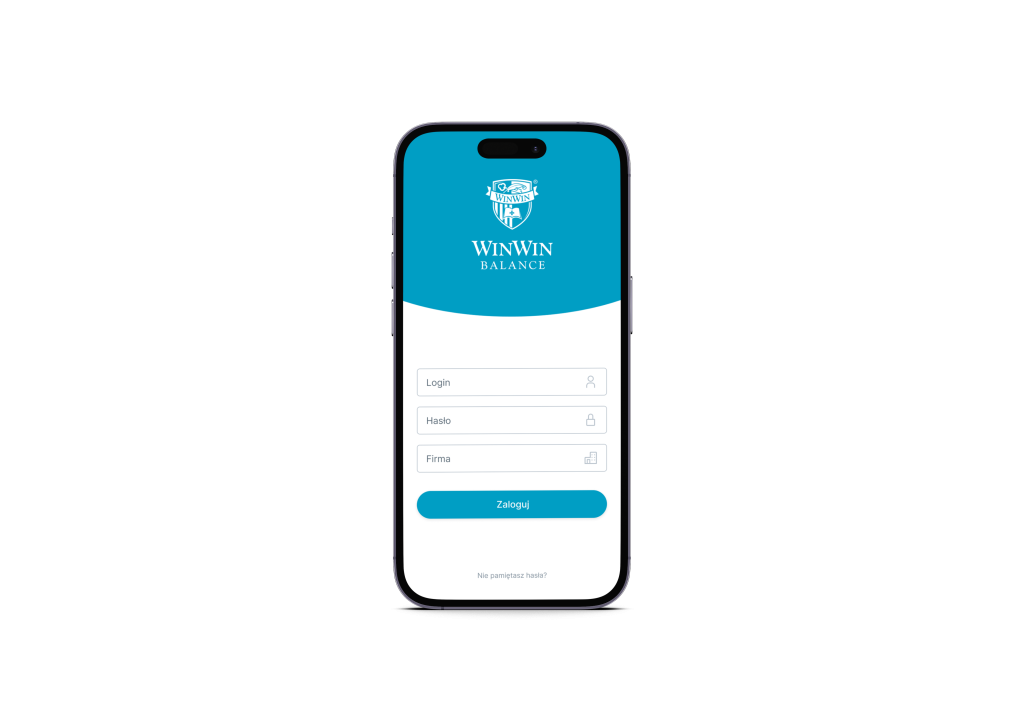