How to Implement 5S: Introduction
Here are five steps that will help you effectively implement the 5S method in your company. In today’s world, where market competition is increasing, every company is looking for ways to improve efficiency and employee engagement. One of the helpful tools in this process is the 5S method. In this article, we will present five steps for effective implementation of the 5S method in your company. We also invite you to familiarize yourself with our other articles on the Kaizen philosophy.
How to Implement 5S: What does the phrase 5S mean?
The name “5S” comes from five Japanese words: Seiri (Sort), Seiton (Set in Order), Seiso (Shine), Seiketsu (Standardize), and Shitsuke (Sustain).
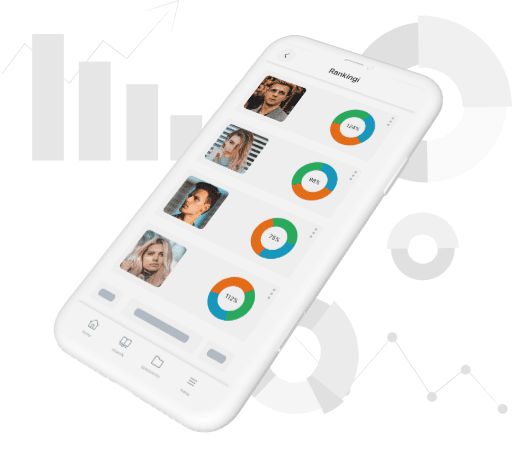
How to Implement 5S: What is the 5S method and how does it work?
The 5S method is a workplace management system aimed at improving efficiency by improving organization and tidying up the workplace.
- The first step in the 5S method is Sort, which involves removing all unnecessary items from the workplace.
- The second step is Set in Order, which involves arranging all necessary items in a way that is easy to find and use.
- The third step is Shine, which involves thoroughly cleaning the entire workplace.
- The fourth step is Standardize, which involves establishing standards for each element of the workplace.
- The fifth and final step is Sustain, which involves maintaining order and cleanliness in the workplace.
Benefits of Implementing 5S: Why should you implement the 5S method in your company?
Implementing the 5S method can bring many benefits to your company. Firstly, it will improve the efficiency and productivity of your workplace. By organizing and tidying up the workplace, employees will be able to find the necessary tools and materials more easily, which will speed up the production process.
Secondly, the 5S method can help improve safety in the workplace. Removing unnecessary items from the workplace will reduce the risk of accidents related to moving around the workplace.
Thirdly, the 5S method can help improve the quality of products or services offered by your company. By standardizing production processes, you can avoid mistakes and ensure the consistency of products or services.
How to Implement the 5S Method in a production company: Step by Step
Step 1: Preparing the team for the implementation of the 5S method is key to the success of the entire process. Employees must be aware of the benefits of this method and be involved in its implementation. One way to engage employees is to conduct training on the 5S method and its benefits for the company. Employees should also have the opportunity to express their opinions on how the workplace is organized and suggestions for improving processes.
Step 2: Assess the current state and set goals
The next step is to assess the current state of the workplace and set goals for the 5S process. Before starting the process, you should thoroughly analyze the current state of the workplace and identify areas that need improvement. Then, you should set goals for the 5S process. The goals should be realistic and achievable, and their realization should bring tangible benefits to the company.
Step 3: Planning and organizing the workspace
In this step, you should plan the layout of workstations and create a system for organizing tools and materials. It is also important to create a visualization of the ideal workplace, which will make it easier for employees to find the necessary tools and materials and ensure consistency in production processes.
Step 4: Implementation and maintenance of order
In this step, you should provide training for employees on each of the five principles and monitor progress in their implementation. The WinWinBalance system comes in handy, which allows youto collect all necessary information in a system that is easily accessible and visible to everyone and helps maintain order, thanks to the possibility of reporting 5S violations. By implementing the WinWinBalance system, maintaining order will become a daily practice for employees!
Step 5: Monitoring and improving the 5S process
The final step is to monitor and improve the 5S process. In this step, you should regularly monitor progress towards goals and measure the effectiveness of the process.
If problems or shortcomings occur, you should implement WinWinBalance which will help you solve this problems.
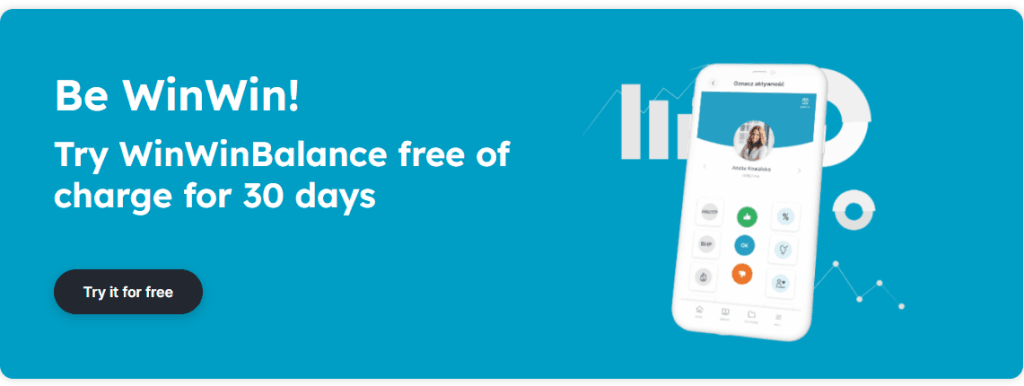
What benefits does implementing 5S bring to a company?
Implementing the 5S method can bring many benefits to your company, such as improving the efficiency and productivity of the workplace, improving safety, and the quality of products or services offered by the company.
Examples of companies that have successfully implemented the 5S method and achieved success
One example of a company that has successfully implemented the 5S method is Toyota Motor Corporation. Toyota has been using the 5S method for many years and has achieved many benefits, such as reducing production costs and improving product quality.
Another example of a company that has successfully implemented the 5S method is Boeing Company. Boeing introduced the 5S method to its manufacturing plants and has achieved many benefits, such as reducing production costs and improving product quality.
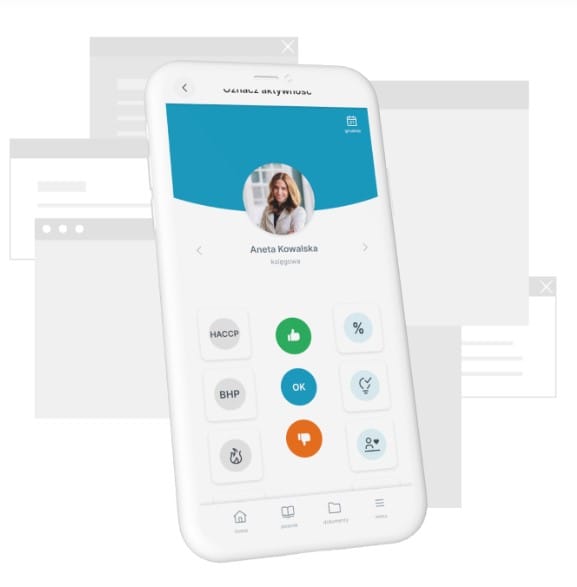
What mistakes should be avoided when implementing 5S?
During the implementation of the 5S method, many mistakes can be made, such as lack of employee engagement or lack of clearly defined goals for the process.
To avoid these mistakes, it is important to engage employees from the very beginning and clearly define goals for the process. To increase employee engagement, we recommend implementing the WinWinBalance system in your organization.